Ralph Walter
1/2/18
I've been meaning to post about this for quite some time. I wanted to show y'all how we show flat paper objects. It's the system I want to show. It came about as a result of some frustration with our former overly-complicated process. I would also like to learn how other institutions deal with these issues. Please tell me how you do this.
From day one, we have used custom made acrylic trays as our default starting point. The trays all have the same 8-hole pattern. We countersink the appropriate set of holes depending on what is needed for the particular installation. The larger of the 4-hole patterns is used with this example. Sometimes we make these in-house but most of the time we outsource them to various local vendors. The hole pattern gives us a point of attachment. There is a lip at the bottom that keeps the object from sliding downward.

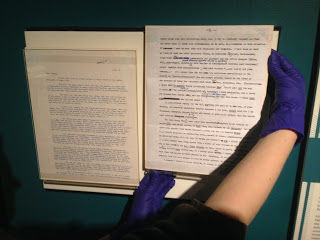
Here is an example of a couple of manuscript pages attached the to acrylic trays. There is a mat board between the object and the tray. The object is held in place to the mat board either with sewn corners, encapsulated in Mylar or sometimes held to the mat board with Mylar straps.
We devised a system to make it MUCH easier when the objects are scheduled for rotations. In situations like this, we attach some special hardware to the exhibit case and the back of the acrylic tray. We use a matched set of dovetail blocks we designed and have 3d printed in plastic. In the photo below, the acrylic tray is on the left and the exhibit case deck is on the right. You can see that there are matching tapered components that slide together for a solid and accurate fit. The tray is installed onto the wall by merely "dropping" it onto the part that is mounted to the wall.
The big advantage to this is that all of the prep work can be done in advance. This means the object along with the mat board and acrylic tray are all assembled and ready to install. When in the gallery, we open the exhibit case, lift off the object along with the tray being swapped and place the new object. The exhibit case is then closed and we're done.

Here are some close-ups of the dovetail blocks. Left: Aluminum nuts are pressed-in to recesses in the 3d printed blocks that attach to acrylic trays. Right: Blocks that attach to a wall or deck have recesses for pan head screws.


Please let me know what you think. Please feel free to share your ideas on possible improvements and how you do this at your institution!
Thanks!
Ralph Walter
MUSEUM OF POP CULTURE 120 6th Avenue N, Seattle, WA 98109 MoPOP.org
Brooks Ward 1/3/18
Are you printing them in-house? What material are you printing in, PLA or ABS (or something else)?They look really great.
Ralph Walter 1/3/18
They are not printed in-house. I used a service called 3d Hubs (3dhubs.com). In a nutshell, with 3dhubs you upload your file and it will show you a list of 3d printing service providers sorted to show the closest ones to where you are, each with an instantaneous bid for their service. I was fortunate enough to be able to use the least expensive service which amazingly had the highest ratings. The male dovetail was just over $6 per piece and the female part was just over $8. I picked them up to avoid shipping cost and turn-around time. Also helpful to know... I had to print several iterations to be able to get the two parts to line up correctly when assembled, making adjustments a few thousandths of an inch each time. The same is true for the hexagonal recesses that hold the aluminum 10-32 nuts.
Pamela Gaible 1/3/18
Re: [mountmaking-forum] Re: 3d printed hardware - used for mounting acrylic trays What materials are they made out of and have the materials been oddy tested? - show quoted text - -- Pam GaibleExhibit Mount Shop Supervisor The Field Museum 1400 S.Lake Shore Dr., 60605 312 665 7368
Ralph Walter 1/3/18
Re: [mountmaking-forum] Re: 3d printed hardware - used for mounting acrylic trays The material is PLA and it has not been oddy tested.
BJ 1/3/18
Re: [mountmaking-forum] Re: 3d printed hardware - used for mounting acrylic trays
Great use of 3D printing. Opens up a lot of possibilities. We've tested some ABS plastic filament that passed oddy- not sure about PLA yet.
Thanks for sharing your design!
-BJ